Revolutionizing System Integration with AI-Powered QR Code Data Capture
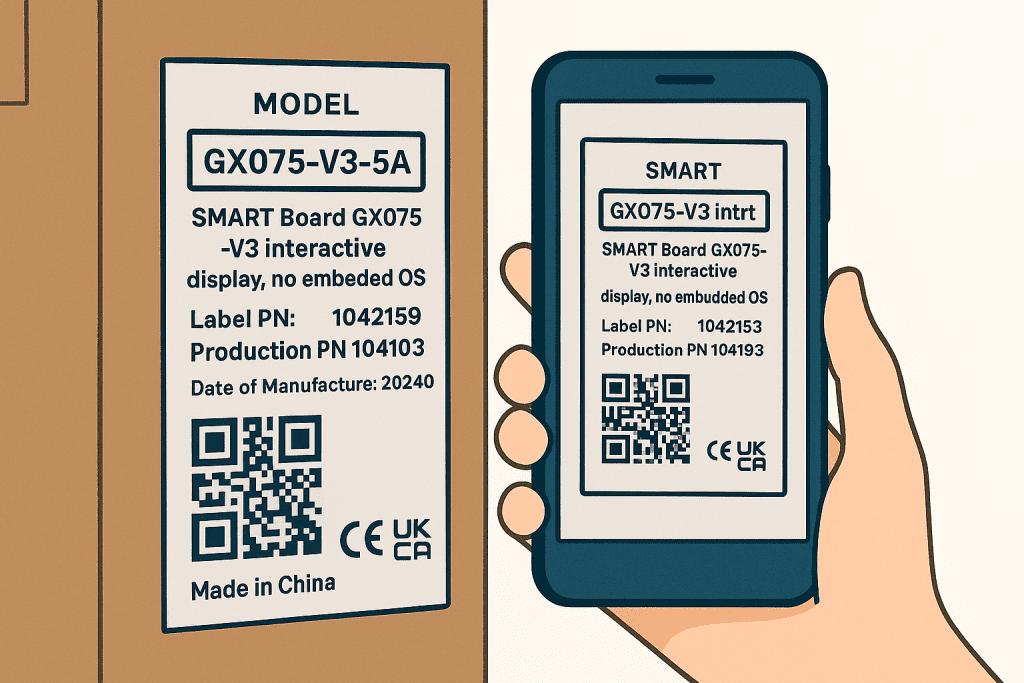
In the fast-paced world of system integration, efficiency and accuracy are paramount. Every minute saved and every error avoided directly impacts project timelines, client satisfaction, and ultimately, profitability. For System Integrators, managing product inventory and onboarding new devices into complex systems often involves a critical, yet surprisingly manual, step: data entry from product labels. While traditional barcodes have served their purpose, they come with inherent limitations that can hinder the very efficiency System Integrators strive to achieve. This is where Integrio.app’s innovative product label extractor, powered by QR codes and advanced Artificial Intelligence (AI), steps in as a true game-changer.
The Limitations of Traditional Barcodes in System Integration
The Limitations of Traditional Barcodes in System Integration
For years, barcodes have been the standard for product identification. They offer a quick way to scan a product and retrieve a single piece of information, typically a product ID. However, in the context of system integration, where a single product might have a multitude of attributes – serial numbers, MAC addresses, model numbers, FCC IDs, and more – traditional barcodes fall short. Extracting this rich, detailed information often necessitates manual transcription, a process fraught with challenges:
- Limited Data Capacity: Standard linear barcodes can only store a small amount of information, usually a product identifier. This means that for every additional piece of data required for a product (which is common in complex integrations), a System Integrator must manually locate and input that information.
- Time-Consuming Manual Entry: As our research has shown, manual data entry is a significant time sink. Employees can spend a considerable portion of their week on these tasks. For System Integrators dealing with numerous products, this translates into hundreds of hours annually spent on repetitive, non-value-added work.
- High Risk of Human Error: The more manual data entry involved, the higher the likelihood of errors. Studies indicate that manual data entry can have an error rate of around 1%. Even a small percentage of errors can lead to significant downstream issues in system configurations, inventory discrepancies, and project delays, costing both time and money.
- Lack of Comprehensive Data Capture: Traditional barcode scanning often leaves a gap in data capture, forcing System Integrators to rely on physical labels or separate documentation for crucial details not encoded in the barcode.
These limitations directly impact the efficiency and accuracy that System Integrators demand, creating bottlenecks in the product onboarding and inventory management workflows.
QR Codes: The Foundation for Unprecedented Tracking and Data Capture
Unlike their linear predecessors, QR codes (Quick Response codes) are two-dimensional barcodes capable of storing significantly more information. This expanded data capacity makes them an ideal solution for the complex data requirements of system integration. A single QR code can encapsulate a wealth of product details, from serial numbers and MAC addresses to model numbers and even links to product documentation or configuration guides. This inherent capability of QR codes lays the groundwork for a more efficient and accurate data capture process.
Integrio.app leverages QR codes not just for identification, but as a comprehensive tracking and data collection mechanism. Before a product even arrives at the warehouse, System Integrators can print out all necessary product QRs and attach them to the product upon its arrival. This proactive approach enables:
- Seamless Product Movement Tracking: From the moment a QR label is attached, Integrio.app provides unparalleled visibility into product movement. System Integrators can check a product into any site as it moves from one location to another, ensuring every touchpoint is recorded. This granular tracking provides full transparency to all stakeholders, a critical advantage in complex integration projects.
- Precise Product Matching: By scanning the QR code, System Integrators can instantly access the exact matched product in the system, eliminating ambiguity and ensuring that all subsequent data collection and updates are tied to the correct item.
- Versatile Data Collection at the Point of Action: Beyond just tracking, the QR code becomes a gateway for diverse data capture. System Integrators can manually collect critical data points such as IP addresses or MAC addresses directly through the app, associating them instantly with the scanned product. The app also supports taking videos and general images, providing rich contextual data for documentation or troubleshooting.
- AI-Powered Label Extraction: A key capability is the ability to take an image of the product label, which is then processed using AI and OCR. This advanced feature extracts all relevant data from the label and adds it against the product, further enriching the product's digital profile without manual input.
The Power of AI-Powered OCR: Integrio.app’s Intelligent Label Extractor
While QR codes provide the vessel for rich data and tracking, the true revolution comes with the integration of AI-powered Optical Character Recognition (OCR) within Integrio.app. This is where the magic happens for System Integrators. Instead of simply scanning a barcode for a single identifier, Integrio.app’s feature allows users to take an image of the product label. This image is then sent to Google Cloud AI for processing, leveraging advanced OCR capabilities to extract all relevant data points from the label.
Here’s how Integrio.app’s intelligent label extractor transforms the process:
- Comprehensive Data Extraction: The AI-powered OCR can identify and extract various data fields from the label, regardless of their format or placement. This includes manufacturer details, model numbers, serial numbers, MAC addresses, FCC IDs, and any other critical information printed on the label. This eliminates the need for System Integrators to manually search for and input each piece of data.
- Seamless Mobile Scanning: The feature is designed for the mobile app, allowing System Integrators to use their existing mobile devices to capture label images. This provides unparalleled flexibility and convenience, enabling data capture directly at the point of product arrival in the warehouse or on-site during an integration project.
- Automated Data Population: Once extracted, the data is automatically populated against the corresponding product within Integrio.app. This direct integration drastically reduces manual data entry, minimizing the risk of human error and ensuring data consistency across the system.
- Real-time Accuracy and Efficiency: By automating the data capture process, Integrio.app ensures real-time accuracy of product information. This leads to immediate updates in inventory records, faster product onboarding, and a significant reduction in the time System Integrators spend on administrative tasks. The time saved can be redirected towards more strategic activities, such as complex problem-solving and system optimization.
Quantifying the Impact: Time Savings and Enhanced Productivity for System Integrators
The benefits of Integrio.app’s product label extractor translate directly into tangible time savings and enhanced productivity for System Integrators. Consider the cumulative effect of eliminating manual data entry for hundreds, if not thousands, of products annually. Research consistently demonstrates the profound impact of automation:
- Significant Time Reclamation: Studies by McKinsey suggest that workflow automation can save employees up to 30% of their time. For System Integrators, who often juggle multiple complex projects, this translates into reclaiming valuable hours previously lost to tedious data transcription. WorkMarket reports indicate that employees estimate a potential time saving of 240 hours per year through task automation. Imagine the impact of these reclaimed hours on project delivery and overall operational efficiency for a system integration firm.
- Boosted Productivity and Accuracy: Over 90% of workers surveyed have reported increased productivity due to automation solutions. By virtually eliminating manual data entry errors, Integrio.app ensures that the data associated with each product is accurate from the outset. This prevents costly rework, troubleshooting, and potential project delays caused by incorrect information. The combination of speed and accuracy empowers System Integrators to work more efficiently and reliably.
- Cost Reduction: The financial implications of manual data entry are substantial, with the average cost of a single data entry point reported at $4.78. By automating this process, Integrio.app helps System Integrators mitigate these recurring costs, contributing directly to their bottom line. Furthermore, the reduction in errors translates to fewer resources spent on rectifying mistakes, leading to further cost efficiencies.
In essence, Integrio.app’s product label extractor empowers System Integrators to move beyond the limitations of traditional methods and embrace a future where product onboarding is fast, accurate, and virtually error-free. This innovative feature is not just about saving time; it’s about transforming the way System Integrators work, allowing them to focus on what they do best: delivering seamless and robust integrated solutions for their clients.
Ready to see Integrio’s AI Label extractor in action?
Arrange a one-to-one demo and trial integrio free of charge for 7 days.
Arrange a demo
Arrange a demo with an expert member of the team today
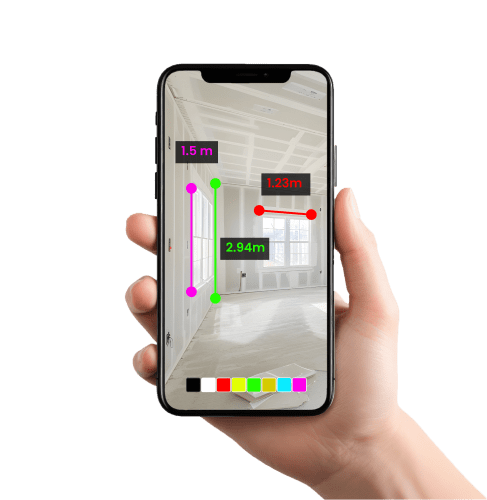